In the world of organizational management, efficiency is key. One of the fundamental methodologies that businesses around the globe, including MMC, have embraced to enhance productivity and organization is the 5S methodology. Initially developed in Japan, the 5S methodology focuses on improving workplace efficiency through the principles of sorting, setting order, systematic cleaning, standardizing, and sustaining. Let’s delve deeper into the steps of the 5S methodology and explore why it is highly beneficial for companies seeking to streamline their operations.
Understanding the 5S Principles:
The 5S methodology comprises the following steps:
1. **Sort (Seiri)**: This step involves separating necessary items from unnecessary items in the workplace. Unnecessary items are removed to create a clutter-free environment, making it easier to locate essential tools and materials.
2. **Set in Order (Seiton)**: Once unnecessary items have been removed, the next step is to organize and arrange the necessary items in a logical and efficient manner. Tools and materials should be placed in designated locations to improve accessibility, reduce search time, and prevent disorganization.
3. **Shine (Seiso)**: The shine step emphasizes the significance of cleanliness in the workplace. Regular cleaning and maintenance of work areas not only enhance safety and hygiene but also contribute to a positive work environment.
4. **Standardize (Seiketsu)**: Standardization involves establishing uniform processes and procedures across the organization. By creating standardized work practices, companies can promote consistency, minimize errors, and improve overall efficiency.
5. **Sustain (Shitsuke)**: The final step in the 5S methodology is sustaining the achieved improvements. Continuous reinforcement of the 5S principles through training, audits, and regular monitoring ensures that the workplace remains organized and efficient over time.
Benefits of Implementing the 5S Methodology:
Implementing the 5S methodology can yield numerous benefits for companies, including:
1. **Improved Efficiency**: By eliminating waste, reducing clutter, and optimizing workflow, the 5S methodology enhances operational efficiency and productivity.
2. **Enhanced Safety**: A well-organized and clean workplace reduces the risk of accidents and injuries, promoting a safer work environment for employees.
3. **Cost Savings**: Streamlining processes and reducing unnecessary inventory can lead to cost savings for the company.
4. **Employee Engagement**: Involving employees in the 5S implementation fosters a sense of ownership and pride in their work environment, increasing employee morale and engagement.
5. **Quality Improvement**: Standardizing work practices and maintaining a clean workspace can lead to improved product quality and customer satisfaction.
The 5S methodology offers a systematic approach to organizing the workplace, improving efficiency, and fostering a culture of continuous improvement. By embracing the principles of sort, set in order, shine, standardize, and sustain, companies can create a more productive, safe, and engaging work environment that ultimately contributes to long-term success.
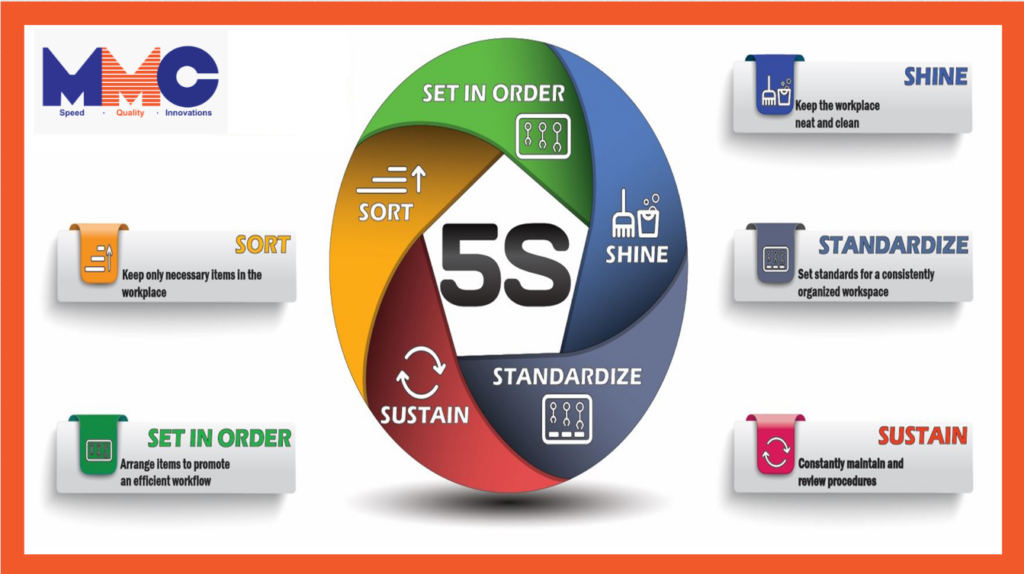