Manufacturing plants are dynamic environments filled with bustling activity, where heavy machinery and complex processes work together to produce goods efficiently. However, this high-energy setting often comes with significant noise levels that pose serious risks to workers’ hearing health. Recognizing the necessity of wearing hearing protection is essential for safeguarding employees and fostering a culture of safety within the workplace.
The primary concern surrounding noise in manufacturing settings is noise-induced hearing loss (NIHL). Prolonged exposure to loud noise can damage the delicate hair cells in the inner ear, leading to irreversible hearing loss. Common sources of hazardous noise in manufacturing include:
- Machinery: Lathes, grinders, and presses
- Tools: Drills and saws
- Material Handling Equipment: Forklifts and conveyor systems
- Impact Noises: Metal striking metal and collisions
NIHL often develops gradually and can go unnoticed until significant damage has occurred. Wearing appropriate hearing protection allows workers to minimize their risk of developing NIHL and preserve their auditory health.
The Occupational Safety and Health Administration (OSHA) sets permissible exposure limits for noise in the workplace. Employers are required to implement hearing conservation programs when noise levels exceed 85 decibels (dB). These programs include:
- Regular monitoring of noise levels
- Comprehensive training for employees
- Provision of suitable hearing protection devices (HPDs)
Non-compliance not only jeopardizes employee health but can also lead to legal ramifications, fines, and increased insurance costs for the organization. By prioritizing the use of hearing protection, employers can ensure adherence to regulations while maintaining a safe working environment.
Wearing hearing protection is not just about individual worker safety; it significantly contributes to overall workplace safety. Elevated noise levels can hinder effective communication, making it challenging for employees to hear warning signals or instructions from coworkers or machinery alarms. Poor communication increases the likelihood of accidents. By using proper hearing protection, employees can enhance their situational awareness, respond quickly to potential hazards, and encourage safer practices across the manufacturing plant.
Promoting the use of hearing protection reflects an organization’s commitment to employee well-being. When workers perceive that their health and safety are prioritized, it boosts morale and fosters a positive work environment. Additionally, preventing hearing loss can result in long-term benefits, including reduced medical expenses and fewer absences due to hearing-related issues.
A variety of hearing protection devices are available, each designed for specific noise exposure levels:
- Earplugs: Disposable or reusable options that fit snugly in the ear canal to block sound.
- Earmuffs: Devices that cover the entire ear, creating a seal that provides additional protection against high noise levels.
- Custom Hearing Protection: Tailored devices crafted to fit an individual’s ear for optimal comfort and effectiveness, particularly beneficial in high-noise environments.
Selecting the right type of hearing protection depends on factors such as noise levels, comfort, and specific tasks performed. Employers should provide thorough training to ensure employees understand how to use and maintain their hearing protection devices effectively.
Wearing hearing protection is essential for safeguarding workers in manufacturing plants against noise-induced hearing loss while enhancing overall safety. By complying with regulations, promoting a strong culture of safety, and prioritizing employee well-being, employers can create a healthier, more productive workspace. Both employees and employers must take proactive steps to protect hearing health, ensuring everyone remains safe and sound in the workplace.
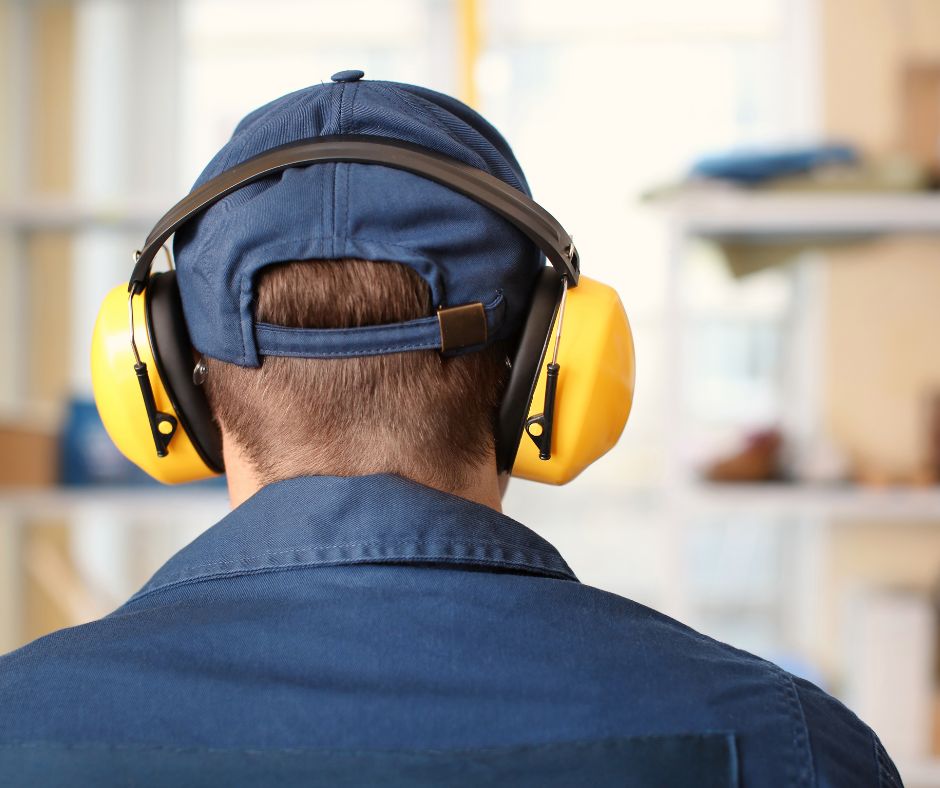