A properly configured Rack Coating System can enable you to reduce damage to parts to save on sorting, scrap and re-work.
The manufacturing of unique and intricate parts requires special attention and processing needs. These parts can come in an array of different sizes, shapes and configurations, which can require special processing and handling needs. To achieve the best corrosion protection and desired appearance, they all cannot be processed in the same manner.
In this article, we will be discussing what is perhaps a better method for applying coatings to fasteners (large, long, and heavy bolts), stampings (that may need soft handling) and assemblies that are complex in design that may have hollow cavities. All these products need excellent corrosion protection and a process that will provide it. With special racking designs and state-of-the-art processing equipment, all these types of parts can get the quality corrosion protection you’re seeking as well as achieving a desirable cosmetic appeal.
Describe the Problem
When processing large, long, and heavy bolts, and depending on the processing methodology, damage can occur on the threads, bearing surface, straightness, and other sensitive areas of the fastener. Additionally, the potential to bend long parts presents the need for special caution in handling during processing. Stampings and assemblies have an equal concern regarding bending and damage during processing. In the coating process, extra precautions need to be taken to ensure that damage does not occur. Of equal importance is the quality of coating being applied during processing. To enable the applied coating to provide the proper corrosion protection, it must be applied evenly and on all surfaces. Here again, special needs may be required if the part being coated has a cavity or pocket, like many stampings do. Each of these types of part damage has an associated cost. Scrap, sorting, re-work and customer dissatisfaction can eat up your profits quickly. There must be a better way!
A Possible Solution
A solution or a better way to address these types of problems may be to process coatings in a Rack Coating System. Now, stating that does not mean all rack coating lines are the same from a quality and efficiency perspective. In our experience, the best methodology for fasteners, stampings, and special parts is a Dip, Drain, Spin (DDS) System. A DDS Rack Coating System, with custom designed racking cassettes, provides an excellent environment to coat parts with the desired results.
The dipping section of the DDS process is just as it implies. We are dipping the parts into a coating solution to ensure complete coverage of the entire part (even in cavities and pockets). The drain section of the DDS process will allow the excess coating to drain off when removing the parts from the coating solution. Of course, if your part has a cavity in it, this will require a drain hole to be part of the part design. The drain hole would be just to allow the captured coating to escape and not be collected into a trapped area.
The spin section of the DDS process is necessary to spin excess coating off the parts and provide more even coat coverage. This is very important for areas like threads when trapped coating could cause a buildup and affect assembling to the mating part. Additionally, this provides a better cosmetic appearance on the part.
Surface Preparation
The surface preparation is absolutely one of the most important steps in any metal finishing operation. It is imperative that the surface on all the parts are properly cleaned and washed to achieve proper adhesion and coverage.
In some rack coating processes, the surface preparation is conducted off-line, and the parts are staged prior to entering the coating process. Depending on the amount of time between cleaning and coating, surface contamination due to the environmental conditions can result in poor adhesion and coverage.
The solution to this is simple. For the best results, have the washing and cleaning steps as an integrated part of the automated system. The parts move directly into the coating bath after cleaning.
Not All Cleaning is Equal
We have found that an alkaline wash followed by a media blast will provide optimum results. Here again, each part type being processed will require its own cleaning cycle, which will be computer controlled to produce the results desired. This will produce very consistent results, part after part, batch after batch.
Material Handling
An additional benefit of a Rack Coating Process is each part is handled only twice. Each part is handled when it is being loaded into the coating rack cassette, and again at the end of the coating process when the parts are unloaded from the rack cassette. This allows for soft handling and a 200% visual sorting out of any foreign material or damaged parts.
Additionally, packaging of the processed parts and components right into the customer’s shipping container could be achieved at the same time, which is an additional time and money savings. This results in zero lost parts and each part gets a free visual inspection. This all equates to cost savings for the manufacturer as well as happy customers.
Each Part Has a Unique Coating Recipe
Production parts come in many sizes, shapes, materials, hardnesses, etc. These variables require the use of a special coating recipe. The recipe would include a specially designed rack/cassette and load size, cleaning cycle, coating times to achieve the correct coating thickness, unique spin cycles, and curing cycle.
In an ideal Rack Coating System, each fastener part or component should have its own recipe, which is computer controlled in order to be reproduced each and every time the parts are processed.
The operator simply scans the part number, and the computer will take over after that. These types of controls will yield consist of results batch after batch. The process would be in control and stable.
Overall, a DDS Rack Coating System line with special design racks will provide an excellent coating system and meet all the customer’s expectations.
At the same time, the DDS Rack Coating System could enable you to reduce damage to parts, which will save on sorting, scrap and re-work.
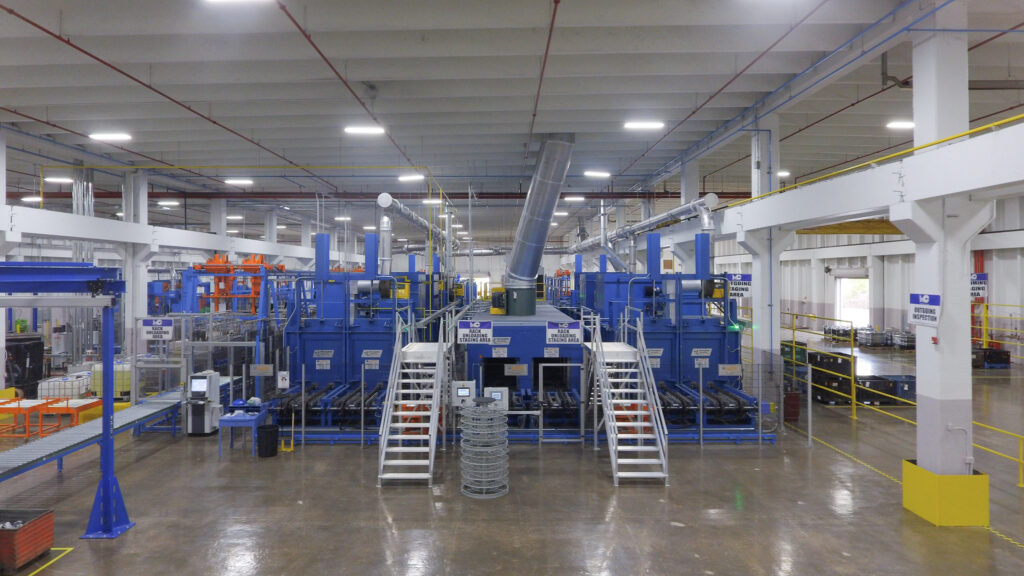