Corrosion testing plays a pivotal role in evaluating the durability and reliability of materials and coatings. Among the various methods available, two widely used techniques are cyclic corrosion testing (CCT) and neutral salt spray testing (NSS). In this article, we will analyze two methods in-depth, including their principles, applications, advantages, and limitations. This will provide a clear understanding of the differences between them.
Principles of Cyclic Corrosion Testing (CCT):
CCT is an accelerated corrosion testing method that simulates real-world environmental conditions by subjecting test specimens to cyclic exposure of corrosive atmospheres, including humidity, temperature variations, and corrosive agents. This technique is measured in cycles and aims to replicate the complex corrosion mechanisms that products experience during their service life, providing valuable insights into material performance and corrosion resistance.
Principles of Neutral Salt Spray Testing (NSS):
NSS, also known as salt fog testing, is a widely used corrosion testing method that involves exposing test specimens to a controlled saline mist environment. The specimens are placed in a chamber where a solution of sodium chloride (NaCl) is atomized to create a corrosive atmosphere. This technique is measured in hours and the purpose is to assess the corrosion resistance of materials and coatings when subjected to salt-induced corrosion, such as that experienced in marine or coastal environments.
Applications:
CCT and NSS find applications in a range of industries, including automotive, aerospace, electronics, coatings, and manufacturing. CCT is particularly suitable for evaluating the corrosion resistance of multifunctional coatings and complex systems, while NSS is commonly used for assessing the initial corrosion resistance of materials and coatings.
Advantages of Cyclic Corrosion Testing:
- Realistic simulation: CCT replicates actual environmental conditions, allowing designers and manufacturers to assess how materials and coatings will perform in real-world scenarios.
- Multifactor testing: CCT exposes specimens to a combination of environmental factors, including temperature, humidity, salt spray, and drying cycles, producing more comprehensive corrosion data.
- Time efficiency: CCT can accelerate corrosion processes, providing quicker results compared to natural exposure or traditional laboratory methods.
Advantages of Neutral Salt Spray Testing:
- Standardized method: NSS follows internationally recognized standards, making it easier to compare results and ensure consistency across different testing facilities.
- Cost-effective: NSS is generally less expensive than CCT in terms of equipment, materials, and operational requirements.
- Simplicity: NSS is relatively easy to set up and conduct, making it an accessible option for small-scale testing or initial assessment of corrosion resistance.
Limitations:
- Representativeness: Both CCT and NSS have limitations in fully replicating the complexity of real-world corrosion environments and the specific mechanisms involved.
- Interpretation challenges: Interpreting test results, especially when comparing different testing methods, can be challenging. Careful analysis and consideration of multiple factors are necessary to draw meaningful conclusions.
Cyclic corrosion testing (CCT) and neutral salt spray testing (NSS) are valuable tools for evaluating corrosion resistance. While CCT provides more realistic simulation and multifactor testing, NSS offers standardized, cost-effective, and simpler testing procedures. The choice between these methods depends on specific testing requirements, industry standards, and the desired level of corrosion resistance assessment. Understanding their principles, applications, advantages, and limitations is essential for making informed decisions and ensuring product durability and reliability in various environments.
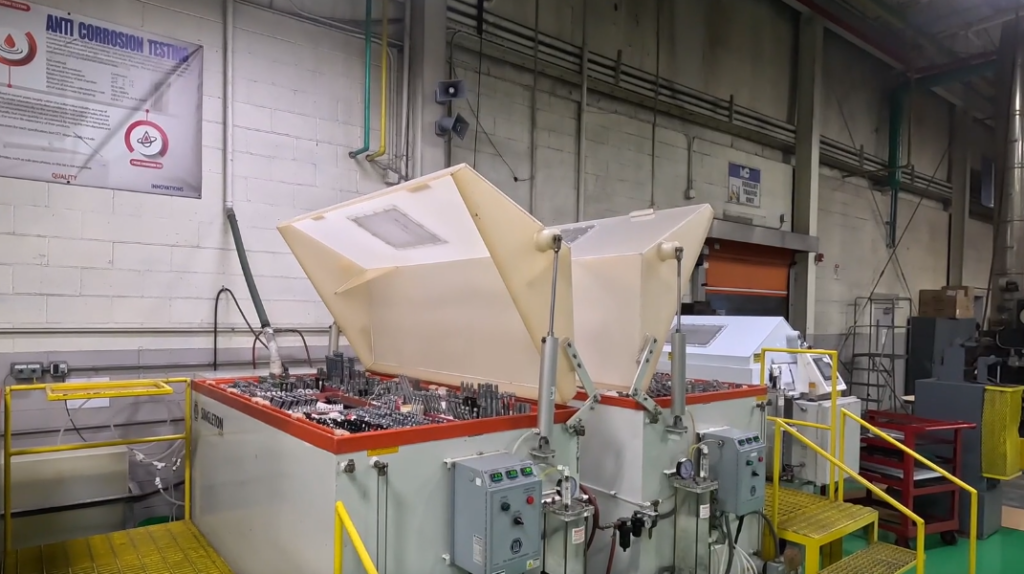